An Introduction to Rotary Friction Welding
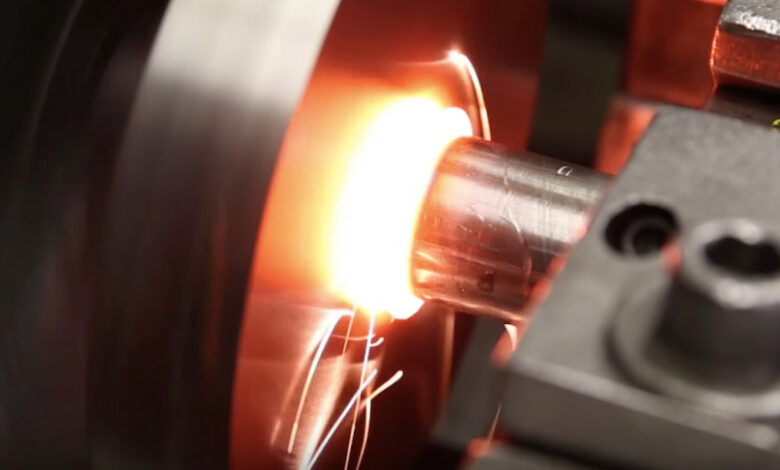
Rotary friction welding is a subset of friction welding. As the name implies, friction is used to join two objects together. Its applications include gas turbine, automotive, aircraft engine turbine and drill pipe manufacturing. Continue reading to learn more about the various materials and methods of rotary friction welding.
Related: Top 5 Welding Skills in High Demand
Usually, the materials welded together are metallic. However, a rotary welder Troy OH can also use thermoplastic polymers. The welding of wood is being explored but not typical of this manufacturing process. If two different materials need to be joined together, an interlayer can facilitate the welding process. This indirect material acts as a bond between the two materials being welded.
There are two standard methods of rotary friction welding:
- In direct-drive friction welding, the motor and spinning chuck are connected. The two objects being welded continuously spin to create heat and then stop with a manual break.
- Inertia friction welding does not involve a continuous spinning action. Instead, one piece is spun on the chuck using a motor and then disengaged. The two materials are then pressed together until the spinning action stops. Force is maintained after the spinning stops to set the weld.
Related: The Importance of the Steel Industry
The steps of friction welding are as follows:
- Steps 1 and 2 are the friction stages. First, the spinning is initiated, then the material is pressed together.
- Step 3 is the braking stage. The material either breaks manually or from a lack of inertia.
- Step 4 is the pressure stage. A forge pressure is applied after spinning has stopped.
- Finally, step 5 is the flash stage. A flash is conducted and cut off by the welding machine.
There are many forms of welding. Rotary friction welding is standard in manufacturing for its accuracy and repeatability. It is an essential facet of many industries and allows modern equipment to be produced on a mass scale.